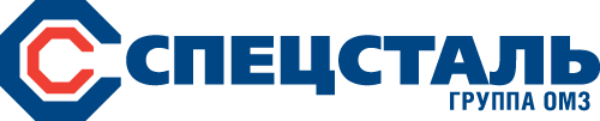
Аудит использования оборудования цеха №20
Цель проекта
Определить возможности пресса 3200 т.с. по максимальному увеличению производства поковок в месяц.
Задачи
1. Проанализировать планово-логистическую составляющую производственного процесса, включая процессы термообработки и адьюстажа, выпуска поковок, брам и «перерубов» в 20 цехе.
2. Проверить правильность существующего коэффициента (0,4), отражающего трудозатраты, связанные с производством брам, по отношению к поковкам.
3. Сравнить экономический эффект от экономии металла при производстве более крупных слитков для пресса 1250 т.с. и потери от перерубов на прессе 3200 т.с.
4. Разработать организационно-технические рекомендации для увеличения производства поковок до 2200 тонн в месяц на прессе 3200 т.с. и определить оптимальную производительность пресса в тоннах на единицу времени.
5. Разработать методику расчета плана ковки и сдачи поковок.
6. Осуществить выборочную проверку выполнения техпроцессов и хронометраж фактических трудозатрат.
7. Определить соответствие структуры и численности персонала существующему и планируемому/ желаемому объему выпускаемой продукции.
Методы
1. Анализ технической документации
2. Интервьюирование руководителей и ведущих специалистов
3. Исследование затрат рабочего времени с помощью фотографии рабочего времени (фотографии рабочего времени оборудования и фотографии рабочего времени работников на прессовом участке 20 цеха ООО «ОМЗ-Спецсталь», пресс 3200 т.с.)
4. Исследование выполняемых технологических операций с помощью хронометража
Результаты
I
Производительность ковки на 3200 т.с. (тонн/час) (как и обратная величина – трудоемкость, час/тонну) определяется:
- временем работы с изделием по КТП к общему фонду рабочего времени, на данный момент составляет 72,9%
- временем обработки по КТП, определяемой номенклатурой (трудоемкостью КТП) и массой поковки, что отражено на нижеприведенных графиках по основным типам КТП
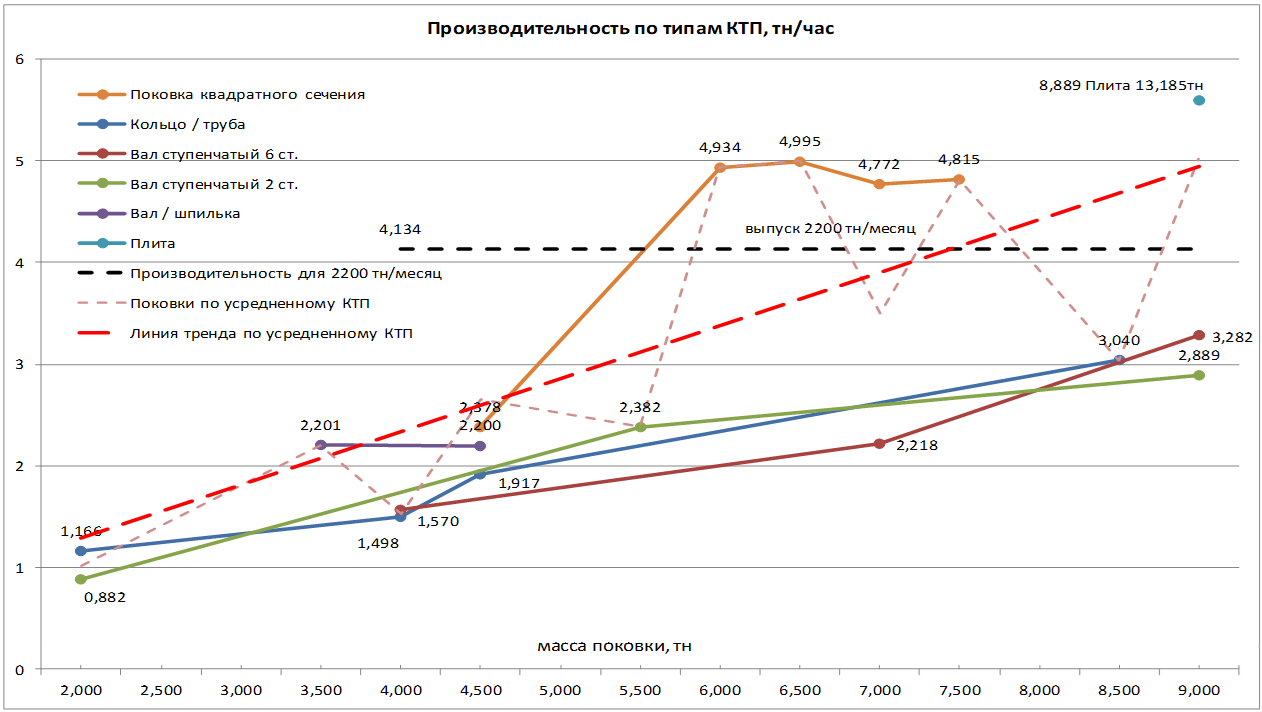
Данные графики показывают, что тоннаж не может быть использован для объективной оценки выпуска по ковке без учета трудоемкости КТП и масс обрабатываемых поковок. Условием для тоннажа, как объективного показателя, является независимость производительности от массы поковок (пример: линия – необходимая производительность для выпуска 2200 тн).
1. Учет трудоемкости для обработки на прессе 3200 т.с. различных типов номенклатуры при планировании запуска в производство.
2. Снижение задействования пресса 3200 т.с. на обработку поковок с массой до 3 тонн и другие неосновные работы
3. Снижение запасов незавершенного производства
4. Другие возможности увеличения производительности
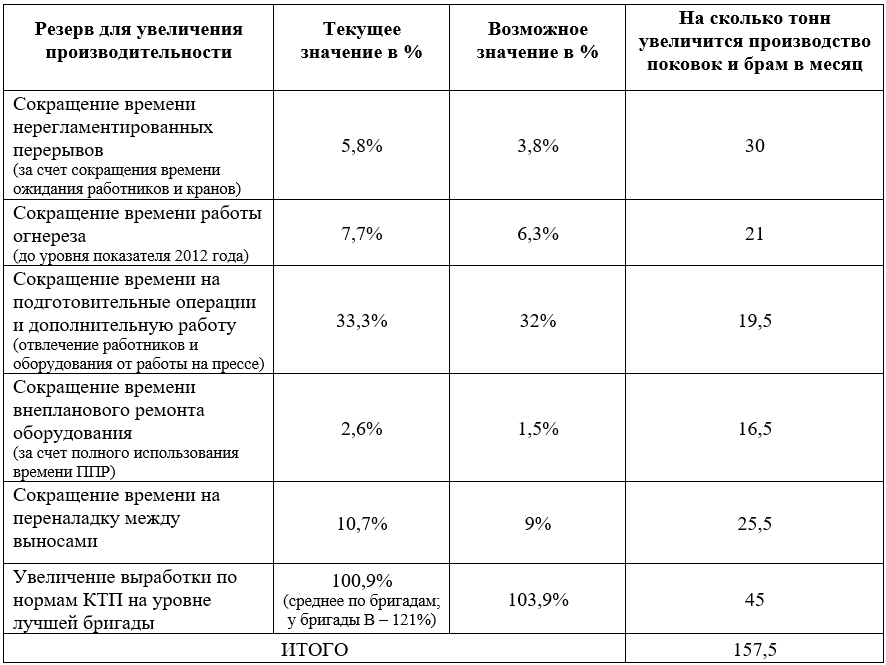
II
Существующий коэффициент (0,4) перевода тоннажа брам в приведенный тоннаж поковок не отражает реальные трудозатраты на производство отдельных типов брам. Сделанные расчеты, основанные на трудоемкости производства различных типов брам позволяют более точно определять приведенный тоннаж наработанный на прессе 3200 т.с.
III
Задача экономического эффекта от переруба не имеет однозначного решения, а зависит от конкретной поковки и имеет комбинаторный характер с выбором слитков из ряда, возможных к выплавке 8-м цехом. Каждый переруб в среднем занимает около 30 минут, что соответствует усредненному времени одного выноса по нормированным по массе для 3200 КТП (производство 1,291 тн). Критерием оптимальности переруба является минимальный процент экономии металла при превышении, которого переруб становится экономически целесообразным.
IV
Имеющихся работников хватает для выполнения текущих задач, однако количество кузнецов, машинистов манипулятора, пресса и кранов минимально возможное. В случае выхода цеха на выпуск более 1700 тонн поковок и брам в месяц и при наличии такой технической возможности целесообразно добавить в штат к уже имеющимся 2-3 рабочих.
V
Планово-логистические составляющие производственного процесса. Основные параметры и выводы по производственному циклу 3200 тс:
- операции цикла соответствуют нормам, определенным в цехе, нет пересечений производственного потока, поток изделий соответствует входу (очередности) на 83%, внеочередное выполнение части заказов в основном вызвано изменениями планирующими органами предприятия сроков сдачи продукции.
- межоперационные интервалы, включая копеж составляют более 10 суток
- общее время цикла 21,18 суток с учетом того, что время операций составляет 48,8%, нуждается в сокращении до уровня необходимого запаса НЗП, обеспечивающим буфер перед ограничивающей операцией ковкой.
В целом планово-логистическая составляющая производственного процесса не является ограничивающим фактором выполнения производственных заданий, за исключением общего времени производственного цикла, содержащего более 50% межоперационных перерывов и необходимого к сокращению. Следствием растяжения общего времени цикла является значительное превышение запасов незавершенного производства над необходимым для обеспечения буфера непрерывности производственного процесса, что приводит к неоптимальному комплектованию печей, превышению времени копежа, ведущего к возможному появлению поверхностных дефектов металла, повышенной вариативности выполнения операций и прочих потерь, связанных с обслуживанием НЗП.
VI
Разработана методика расчета плана ковки и сдачи поковок на основе производительности трёх цехов.
VII
В цеху имеется высокий уровень организации производственного процесса: стабильный, ритмичный, многолетний выпуск продукции требуемого качества; фактическая выработка соответствует КТП; нерегламентированные потери времени сведены к минимуму.
Также в цеху создана особая корпоративная культура, способствующая продуктивной производственной деятельности и создающая положительную мотивационную атмосферу среди работников.
Разработка модели трудоемкости цеха №8
Общие выводы
1. На данный момент количество персонала является достаточным как для сохранения текущего выпуска кузнечных слитков, так и для увеличения выпуска сортовых до 5000 тонн и более, и основной задачей является сохранение существующего штата квалифицированных рабочих и его своевременное пополнение при имеющих место невыходах и текучести кадров.
2. Для увеличения объема выпуска сортовых слитков до 6191,2 тн при сохранении существующей пропорции (65% - 35%) марок стали с коротким (СТ 20) и длительным периодами остывания необходимо повысить ритмичность осуществления подготовительных операций и разливки стали. План-график такого построения работ приводится в Приложении 4.1. При выходе на такой объем достаточно только имеющихся в цехе ресурсов: 2-3 подготовителя сталеразливочных канав, задействованные оснастка и площадки, термоса, действующие краны и плановый график разливки кузнечных слитков.
3. Возможно повышение выпуска сортовых слитков до 7429,44 тн за счет увеличения объема СТ 20 до 4952,96 тн при сохранении объема сталей с длительным периодом остывания на уровне 2476,48 тн при увеличении количества подготовителей сталеразливочных канав до 3-4 человек на 2 пролете. Дальнейшее увеличение количества рабочих не приведет к росту объемов, так как узким местом в работе 2 пролета станет наличие имеющейся в цеху оснастки.
4. Максимально возможный выпуск стали только с длительным периодом остывания составляет 3885,88 тн. Для роста объемов выпуска таких сталей, в первую очередь, необходимо будет увеличить количество термосов или количество оснастки.
5. Возможный выпуск только стали 20 составляет 7555,9 тн в месяц при имеющихся в цехе ресурсах: 2-3 подготовителя сталеразливочных канав, задействованные оснастка и площадки, действующие краны и плановый график разливки кузнечных слитков. Максимально возможный выпуск стали 20 составляет 9782,94 тн и потребует увеличения количества рабочих до 3-4 человек и согласования графиков разливки сортовых и кузнечных слитков.
6. Уменьшение коэффициента учета работ, не охваченных нормированием (1,46) и снижение нерегламентированных перерывов (30,1% фонда рабочего времени) будет свидетельствовать о совершенствовании организации производственного процесса и выхода на максимальный уровень выпуска продукции.
7. Рассчитанная фактическая трудоемкость, требующаяся для осуществления 1 плавки сортовых слитков (19,1 час) позволяет более точно связать объем выпуска продукции с необходимым персоналом и усовершенствовать процедуру планирования для создания ритмично работающего производственного процесса.
8. Использование в планировании работ в цехе графиков выпуска сортовых слитков, основанных на повторяющихся циклах, позволит повысить ритмичность загрузки подготовителей сталеразливочных канав.
9. Необходимо проанализировать возможность повышения сопряженности деятельности ПДУ с планированием и организацией работ в цехе.
10. Условная экономическая самостоятельность цеха может вступать в противоречие с целями предприятия, что требует дополнительного рассмотрения имеющихся плюсов и минусов существующей системы.
Модель расчета производительности цеха:
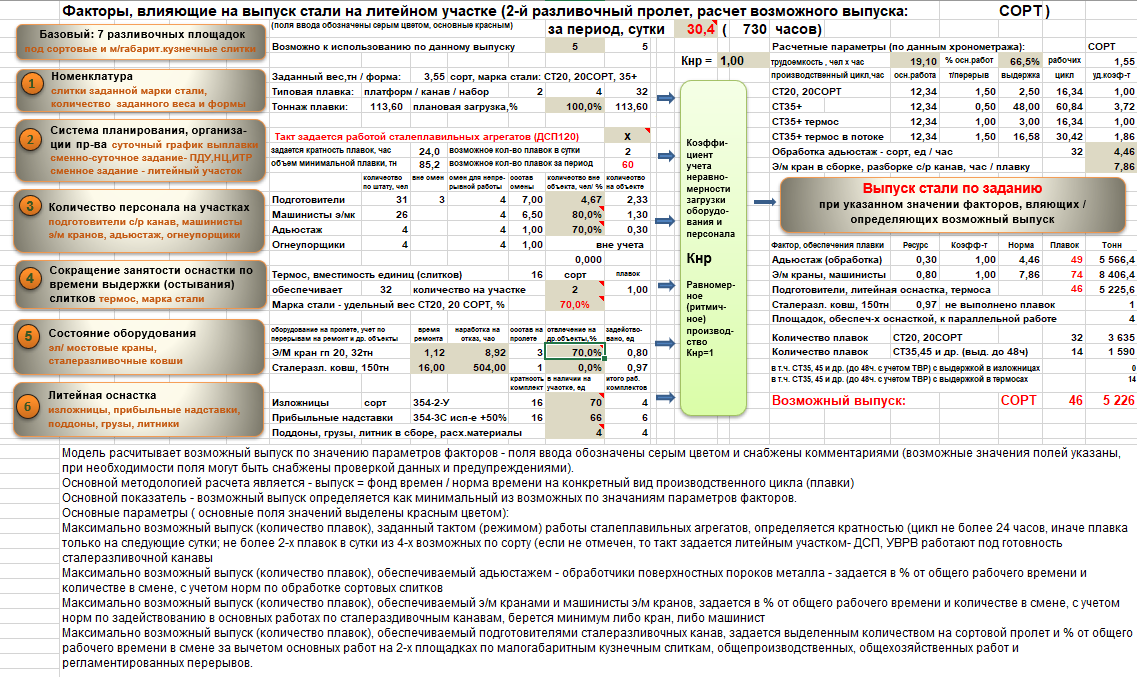
Модель расчета трудоемкости цеха:
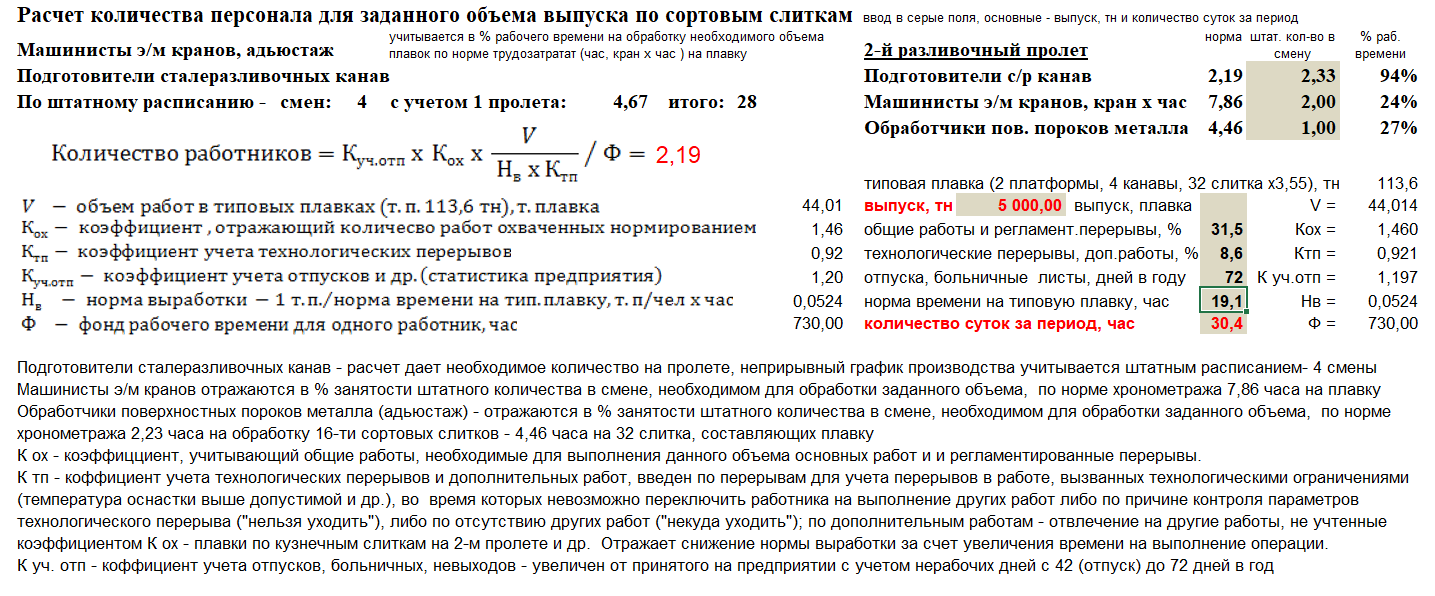
Аудит использования оборудования цеха №15
Общие выводы
1. Производственная система по выпуску листового проката АК является единичным поточным производством.
2. Производственная система по выпуску листового проката АК, являясь единичным поточным производством, не может работать быстрее самой медленной своей составляющей. Производственный участок зачистки, работающий с минимальной производительностью, задает темп всему процессу, являясь для него ограничивающим фактором (узким местом).
3. В управлении системой достаточно контролировать технологический процесс между его первой и ограничивающей операцией. Любые простои на ограничивающей операции не могут быть компенсированы, и для их предупреждения перед операцией необходим резервный запас – внутренний буфер перед ограничением.
Рекомендации
1. Снизить объемы незавершенного производства до 400-500 тонн по всем видам проката, определить буфер перед операцией зачистки в 8 листов.
2. Ввести учёт движения НЗП к сдаче через спавку, отражающую положение каждого листа НЗП, на утреннем рапорте у начальника цеха.
3. Для каждого листа на маршруте принять меры по непревышению длительности выполнения операций НИЦ (7 дней), правки и сокращению интервалов между ними.
Для поддержания необходимой производительности на участке зачистки необходим системный подход:
1. Технико-эксплуатационные меры:
- Профилактическое обслуживание оборудования, сохранение текущего планирования и проведения ППР, присутствие ремонтных служб в любое время работы оборудования с целью недопущения простоев и поломок машин.
- Совершенствование инструмента и оснастки. Техническая экспертиза специалистами цеха, представителями бригад, учет уже имеющихся предложений по вопросам – опорная зона для тонких листов (недопущение деформации листа при обработке), хотя бы на двух машинах, водоотвод и прочие предложения.
2. Организационные меры:
- Выравнивание машинного времени бригад и увеличение его до 80%.
- Внедрение средств визуального контроля и информирования.
- Улучшение гигиенических условий труда – освещение, шумоподавляющие перегородки.
- Поддержание порядка, постоянное улучшение. Превращение сотрудников в сторонников, а еще лучше в активных участников процесса улучшения.
Схема работы цеха 15:
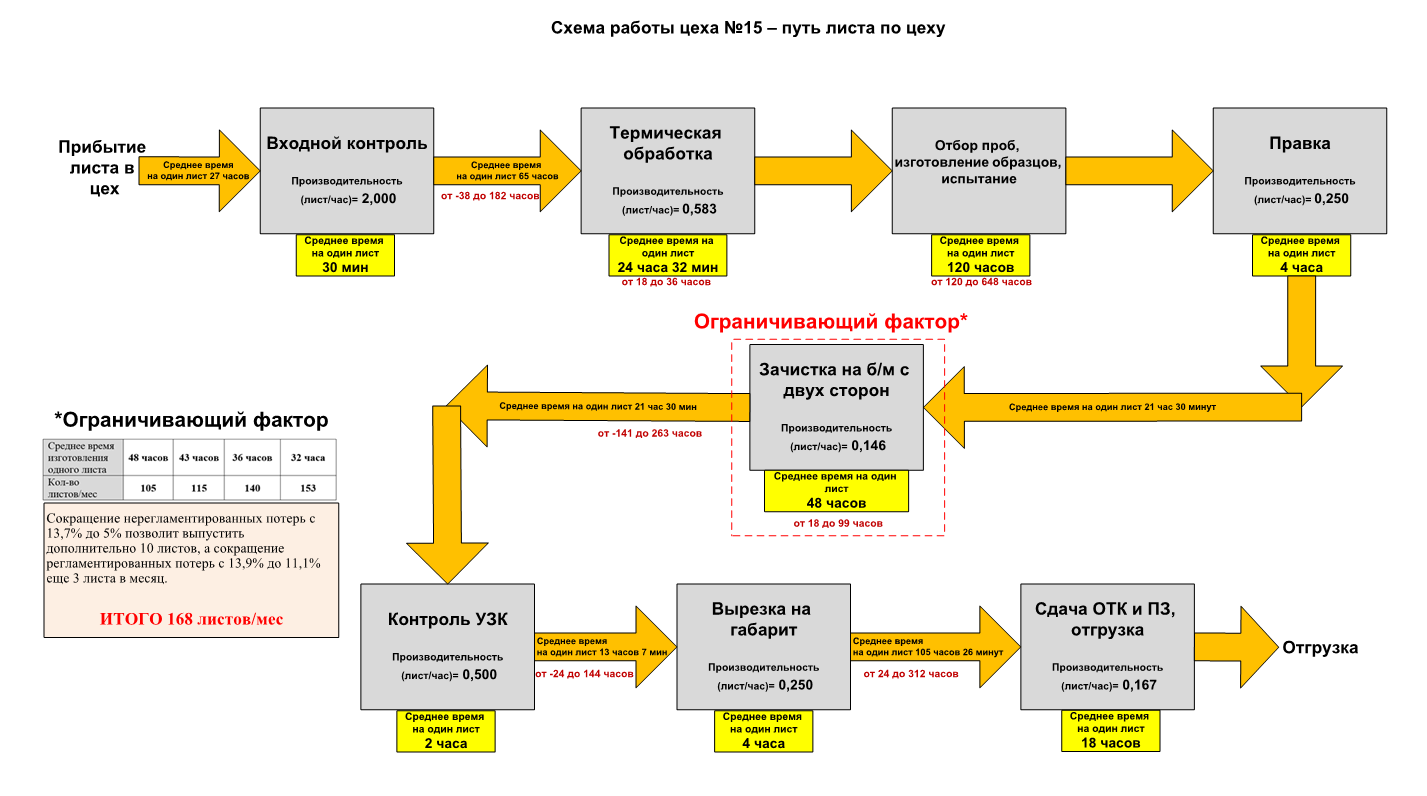